MEMS vs. Geophone
- Introduction About MEMS technology
- MEMS vs. Geophone Technology: A Quick Comparison
- Vibration monitoring sensors for construction: MEMS vs. Geophone
- MEMS vs. Geophone The evolution of vibration measuring equipment
- MEMS vs. Geophone MEMS sensors in vibration monitoring
- MEMS vs. Geophone Requirements and guidelines for vibration monitoring sensors
- MEMS vs. Geophone MEMS Research of Martijn van Delft & Carel Ostendorf
- The Future Of Vibration Monitoring Conclusions
- MEMS vs. Geophone When to use MEMS-based vibration monitoring devices?
MEMS technology has been thought to be inferior in vibration monitoring, in contrast with the supposed more precise readings from sensors using geophone technology. Some state that geophones' measurements are more accurate in low frequencies, whereas others claim to see differences at high frequencies. This is simply not true. Such discrepancies might have existed in the past, but MEMS technology has evolved significantly, and its performance now is equivalent to or even outperforms geophones. MEMS technology surpasses geophones in many ways. Because of the lightweight, compact size and the fact that MEMS technology doesn't require manual leveling, it offers a fantastic basis for developing incredibly easy-to-use vibration monitoring systems.
MEMS vs. Geophone Technology:
A Quick Comparison
MEMS (digital technology) |
Geophone (analog technology) |
✅ Long-Term Accuracy: Maintains accuracy without drifting; calibration is needed only for compliance. Calibrate every two years. |
➖ Accuracy Declines: Accuracy drifts, requiring frequent recalibration. Calibrate annually, or after every project. |
✅ Built to last: Extremely robust. Stays calibrated even after bumps or drops. Always get high-quality measurements. |
➖ Fragile & Vulnerable: Highly sensitive to impact or drops, requiring recalibration. Uncertain measurement quality post-impact. |
✅ Self-Aligning Automatic alignment of axes for perfect readings. |
➖ Manual Alignment: Requires precise manual leveling and alignment of axes. If the device gets bumped, it needs leveling again. |
✅ Compact & Portable: Extremely easy to carry and transport. |
➖ Bulky & Complex: More cumbersome to transport. |
✅ Interference-Free: Not sensitive to magnetic and electrical fields. |
➖ Magnetic Sensitivity: Prone to interference from magnetic and electrical fields. |
✅ Install Anywhere: Mount at any angle; it always provides reliable measurements, regardless of how it's attached. Quick and easy to set up. |
➖ Tricky Setup: Needs to be perfectly level and aligned, making installation time-consuming. The quality of the measurements is not guaranteed. |
MEMS vs. Geophone
For many years, vibration monitoring sensors in the construction sector were predominantly based on geophone technology. In recent years, the introduction of MEMS-based sensors has revolutionized the industry. Gradually, a shift is being made to use these compact and user-oriented devices based on MEMS technology. However, in some cases, the preference for geophones remains, and using MEMS-based sensors in construction is frowned upon or rejected. In this article, we impugn those 'common beliefs' and present evidence from a Dutch scientific research paper where MEMS accelerometers and geophones are compared.
"MEMS sensors will displace geophones."
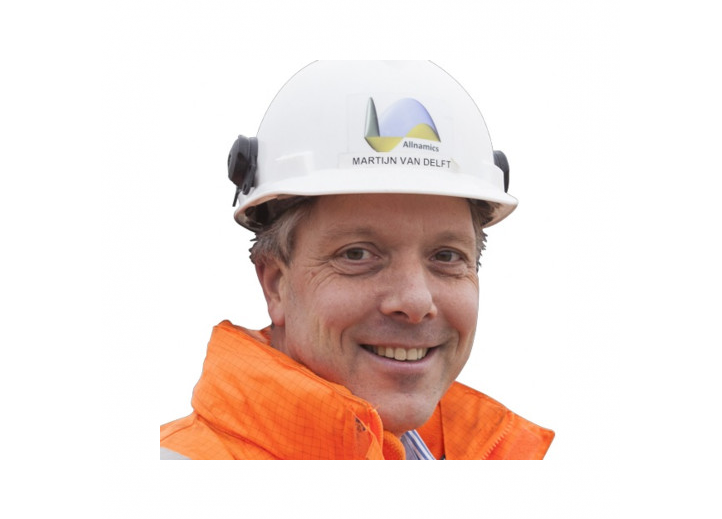
Martijn van Delft
Monitoring Specialist
Allnamics Pile Testing Experts BV
The evolution of vibration measuring equipment
Vibration monitoring is a rapidly evolving field, and its development in the Netherlands has been particularly notable. Because a Dutch monitoring specialist wrote the research article about the Dutch market, we will explore how vibration monitoring systems have advanced over time to meet the needs of Dutch businesses specifically.
The first vibration monitoring devices differed significantly from those available today. In the past, vibration measurement was not a straightforward task. It required linking separate acceleration sensors to charge amplifiers and then connecting those to an analyzer or computer AD card. The measurements were taken over several seconds before finally storing and displaying data with the help of special software.
In 1992, a newly introduced VM system (IFCO) allowed continuous measurements. It was considered a significant modernization, but the device was rather large, consisting of a measuring head with three geophones and a logger.
Between 1995 and 2016, improved vibration monitoring devices entered the market. Solutions with external modems for remote reading, devices with built-in modems suitable for all SBR guidelines, or vibration monitoring sensors with integrated modems and software allowing for live monitoring and automatic reporting have been introduced.
In recent years, MEMS-based sensors have successfully entered the market for construction vibration monitoring, such as the SWARM from Omnidots. Leveraging MEMS technology, vibration monitoring systems are now more accessible than ever - they are easy to install, lightweight, and smaller. Additionally, users often lean towards fully integrated SaaS-based monitoring solutions, with monitoring equipment and a stable, constantly accessible cloud-based platform.
MEMS sensors in vibration monitoring
MEMS is an abbreviation for 'microelectromechanical systems.' MEMS technology allows for the manufacturing of microscale devices such as sensors. Various sectors apply this technology, from aircraft and automotive to even the pharmaceutical industry. MEMS technology revolutionized the sensor market. The miniature devices manufactured on silicon chips are highly reliable and rapidly responding.
Myths about MEMS technology
Still, in the vibration monitoring sector, it is sometimes believed that MEMS-based sensors are inferior to geophones. Some claim that at low vibration levels, MEMS' measurements are not as precise as geophones' and that very high vibration levels are registered by MEMS at high frequencies, compared to a geophone.
This is simply not true. Such discrepancies might have existed in the past, but MEMS-based sensors have evolved significantly since then, and their present performance is equivalent to geophones. MEMS-based sensors surpass geophones in many ways. Because of the lightweight, compact size and the fact that MEMS technology does not require manual leveling, it offers a fantastic basis for developing incredibly easy-to-use vibration monitoring systems. In contrast, the installation of geophones often includes complicated procedures and tiresome training sessions, making it nearly impossible to perform for a non-specialist.
“It is, therefore, crucial that the sensor you choose is suitable for the activity and specific situation related to your project. ”
Requirements and guidelines for vibration monitoring sensors
Some vibration monitors are specifically designed for construction vibration monitoring. Others have a different focus (e.g., machine health monitoring) and are less or even unsuitable for the construction environment. It is, therefore, crucial that the sensor you choose is suitable for the activity and specific situation related to your project. There is no one-size-fits-all solution. Construction vibration monitoring devices are designed to follow certain regulations. Vibration limits are hardly ever set by law; they are generally set by regulations, guidelines, industry standards, and specifications. Often, they differ per country or even per state. In the USA, there is no national standard; therefore, European standards are often applied instead.
For this article, the Dutch standard SBR-A is evaluated. SBR-A includes the following requirements:
Vibration monitoring sensors must have the means to register velocities between 0.2mm/s and 50 mm/s over the entire frequency range of 1 to 100 Hz. For accelerometers, those values have to be between 1 mm/s2 and 30 m/s2.
This standard allows for an accuracy of 10% (which equates to 1dB) over the entire frequency range. A sensor is approved when it complies with those parameters.
MEMS Research of Martijn van Delft & Carel Ostendorf
In 2018, research conducted by Martijn van Delft (Allnamics) and Carel Ostendorf (Cauberg-Huygen) put an end to the skepticism surrounding the use of MEMS for construction vibration monitoring. The vibration monitors Axilog II, Vibra, Infra C22 (geophone technology), and SWARM (MEMS technology) were compared on measurements of two types of vibrations:
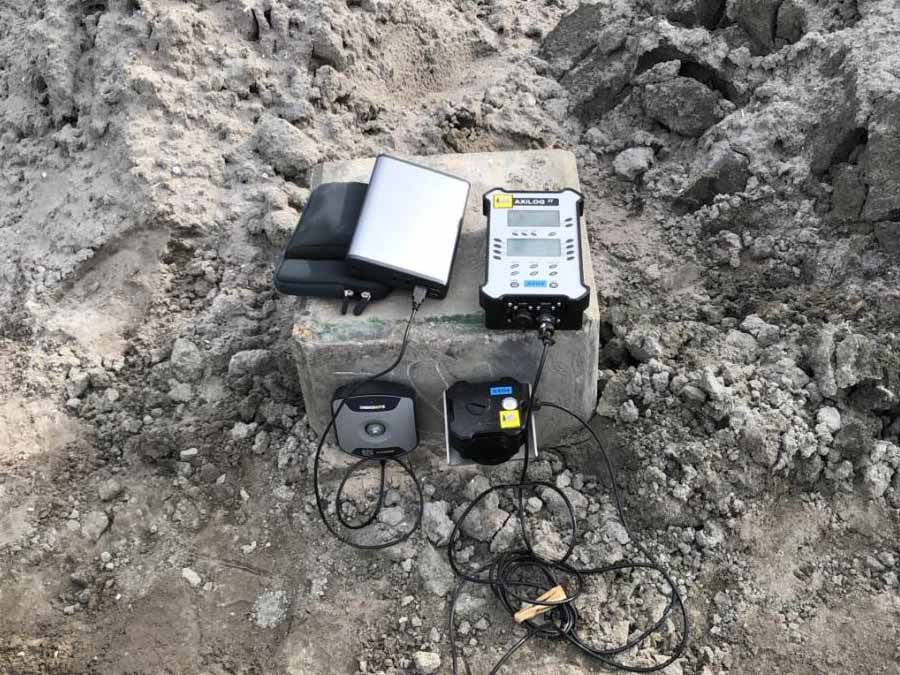
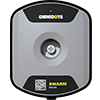
The repeated short period of vibrations (whole series of piling blows)

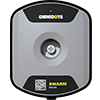
Continuous vibrations (vibrating out a sheet pile wall)
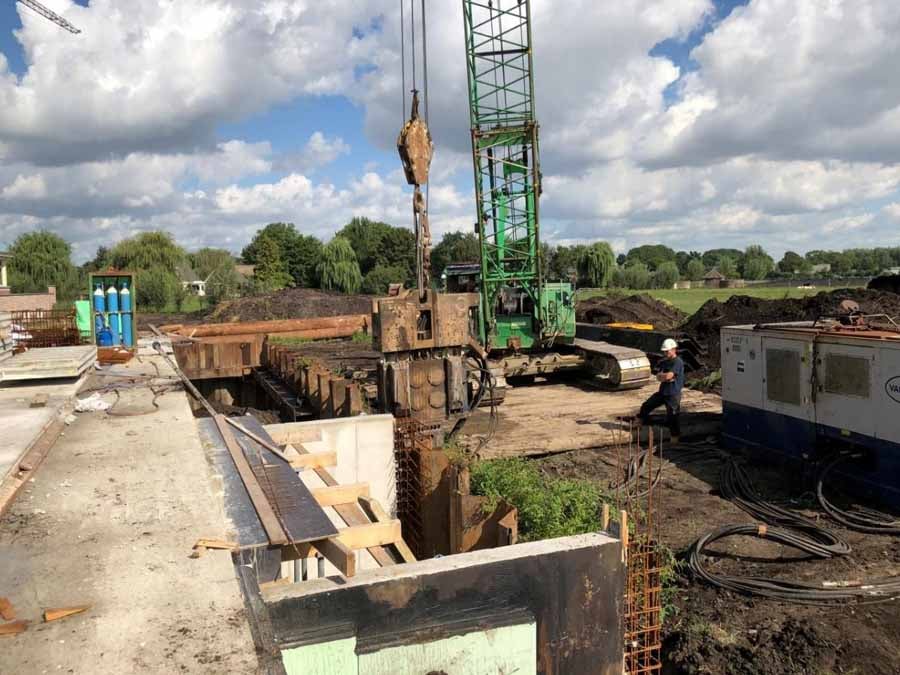
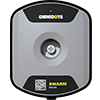
Continuous vibrations (vibrating out a sheet pile wall)
Conclusions
We hope this article has addressed any questions you had about using MEMS-based sensors for construction vibration monitoring. Research confirms that MEMS sensors deliver vibration data as reliably as geophones, yet they provide distinct benefits. Their simplicity, cost-effectiveness, and efficiency make MEMS the future of vibration monitoring.
When to use MEMS-based
vibration monitoring devices?
MEMS-based sensors are suitable for construction work and nuisance, structural health monitoring, and traffic monitoring. They work particularly well in projects where:
- You want to benefit from remote monitoring
- Less experienced people install a vibration monitor
- Real-time insights and remote access are crucial
"With the same number of people, and in the same amount of time, we can now place three or four times as many monitoring devices as with the older systems."
- Tom Smits, Quattro Expertise
Are you considering MEMS technology in vibration monitoring devices for your project? We are pleased to answer any questions you may have regarding that topic.
Contributors:
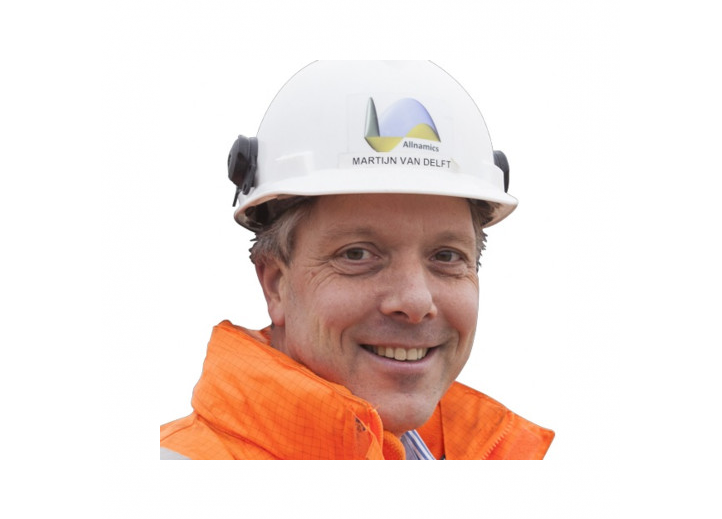
Martijn van Delft
Monitoring Specialist
Allnamics Pile Testing Experts BV
Sources:
Share this article
From Our Blog
Stay up to date with what is new in our industry, learn more about the upcoming products and events.
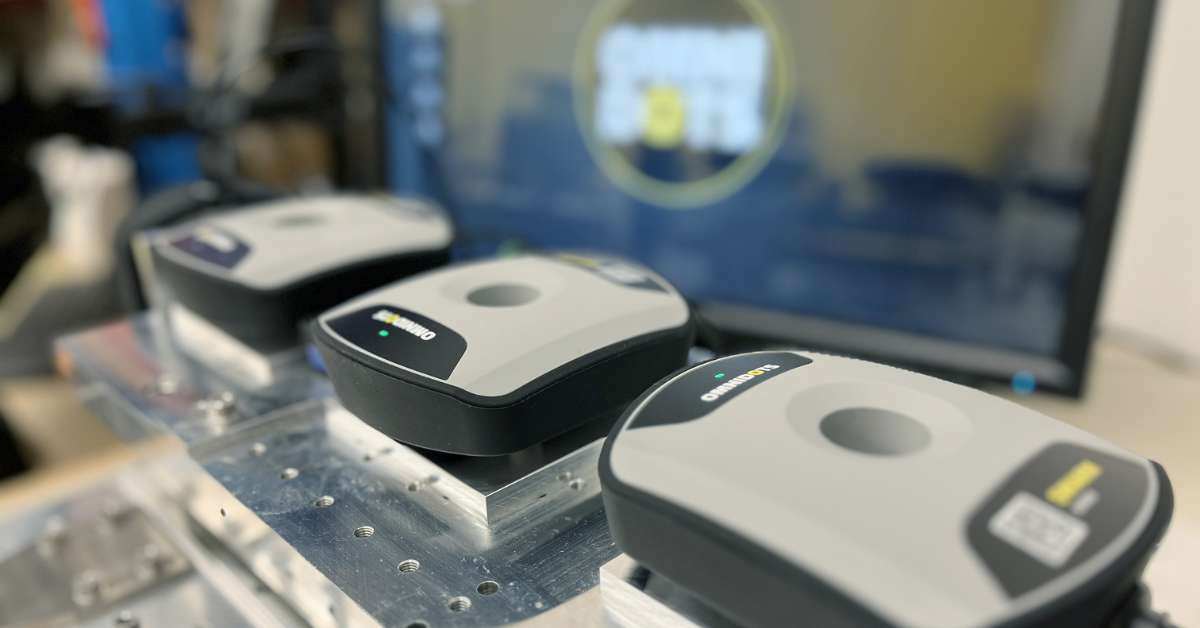
Calibration Frequency: Geophone vs SWARM Vibration
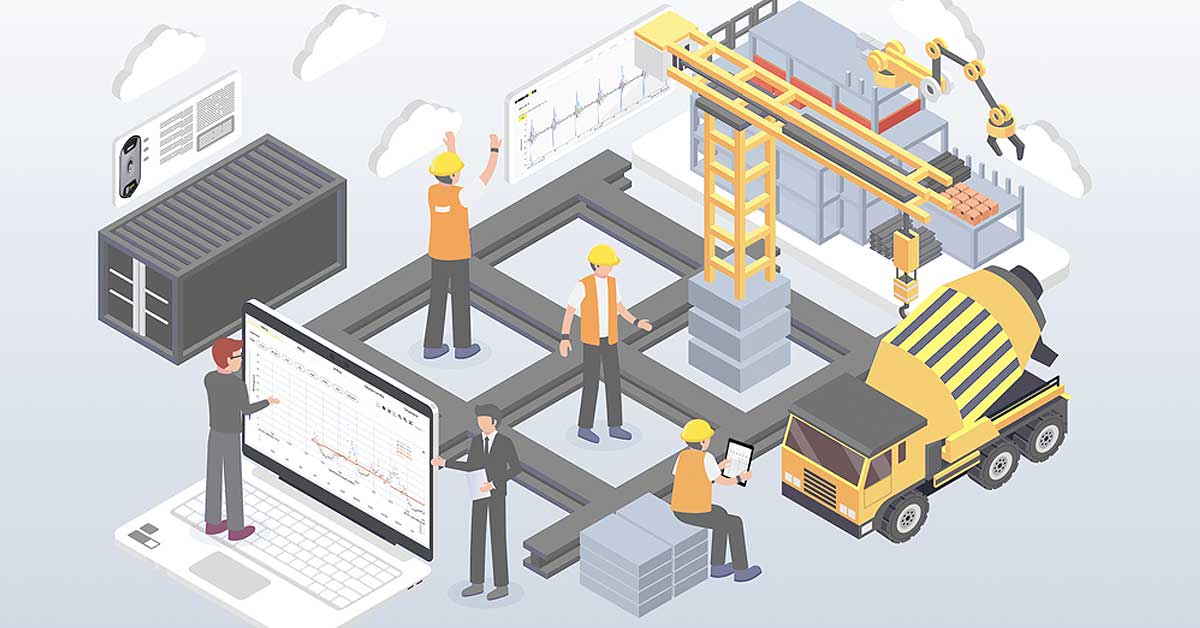
Join Omnidots on a Journey to a Smarter World: INTERGEO 2023
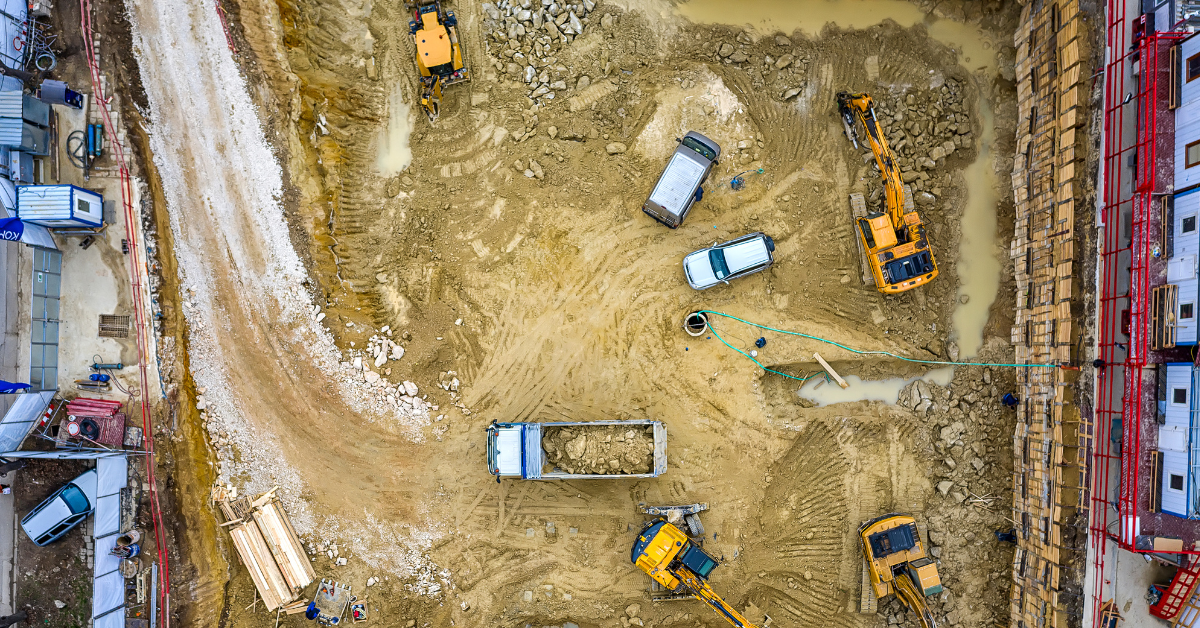